Reliable Battery Tester: How Do We Ensure Product Quality and Stable Performance?
Battery testers are an essential tool in many industries, from automotive and electronics to renewable energy and home applications. Their role in assessing the health, capacity, and functionality of batteries cannot be overstated. A reliable battery tester ensures that batteries perform optimally, avoiding potential failures that could lead to expensive repairs or safety hazards. In this comprehensive guide, we will explore the critical aspects that contribute to the reliability and performance of battery testers, and how manufacturers ensure these products meet high standards of quality and stability.
1. The Importance of Reliable Battery Testers
The importance of a reliable battery tester lies in its ability to assess a battery's state of charge, internal resistance, and overall health. Whether you're testing car batteries, rechargeable devices, or industrial power cells, accurate results are crucial for ensuring the battery will perform as expected. A malfunctioning or inaccurate tester can lead to incorrect diagnostics, potentially causing downtime, safety risks, or even the replacement of perfectly functioning batteries.
In industries like automotive, aviation, and energy storage, battery failure can be catastrophic, leading to costly damage or safety issues. Reliable battery testers help avoid these risks by providing precise data on battery performance, allowing users to make informed decisions about battery maintenance, replacement, or usage.
2. Key Features of a Reliable Battery Tester
A high-quality battery tester must possess several key features to provide accurate, consistent, and useful results. These include:
- Accuracy and Precision: The tester must provide precise readings that are close to the actual battery's performance characteristics. Accuracy in measurements like voltage, capacity, and internal resistance is essential for reliable results.
- Wide Compatibility: A good tester should be able to handle a range of battery types, from alkaline and lithium-ion to lead-acid and NiMH batteries. This ensures its utility across different applications.
- Ease of Use: Intuitive user interfaces, clear displays, and easy-to-understand instructions are essential. Users should not struggle with complex settings to get reliable results.
- Durability: Since battery testers are often used in industrial or field settings, they need to be durable and resistant to shock, moisture, and other environmental factors.
- Portability: Many testers need to be portable, especially for field service or on-site diagnostics. Compact designs and lightweight construction are significant advantages.
- Advanced Features: Higher-end models may include additional features like Bluetooth connectivity, data logging, and cloud-based storage for analysis and reporting, which enhances the tester's usefulness in long-term battery management.
3. Quality Control Measures in Battery Tester Manufacturing
Ensuring the quality of a battery tester begins with a rigorous manufacturing process. Manufacturers implement several quality control measures to guarantee that each unit meets the necessary performance standards. Some key practices include:
- Component Selection: The quality of components used in the tester directly impacts its performance. High-grade sensors, durable casings, and precise circuit boards are selected to ensure long-lasting reliability.
- Assembly Process: Manufacturers must adhere to strict assembly guidelines to avoid defects. Automated systems are often used alongside manual checks to ensure that every tester is correctly assembled.
- In-House Testing: Battery testers undergo in-house testing at various stages of production. This can include electrical testing to ensure accuracy, durability testing to assess resistance to wear and tear, and performance testing to evaluate functionality under different conditions.
- Supplier Audits: Manufacturers often perform audits on their suppliers to ensure that the raw materials and components meet industry standards. This reduces the chances of defects originating from poor-quality parts.
4. Pre-Delivery Inspection and Testing
Before battery testers reach customers, they undergo a pre-delivery inspection process to ensure that they meet quality standards. This phase typically includes:
- Functionality Tests: Each unit is tested under real-world conditions to ensure that it functions as intended. This may involve testing the battery tester’s ability to correctly measure battery voltage, capacity, and internal resistance across different battery types.
- Software Testing: For digital testers, the software that drives the device is rigorously tested for bugs, errors, and performance issues. Software updates or patches are applied as needed to improve the user experience and functionality.
- Compliance Testing: To ensure that the product adheres to international standards, it may undergo certifications and compliance checks related to safety, electromagnetic compatibility, and environmental guidelines.
- Visual Inspection: A final visual inspection checks for cosmetic defects like scratches, loose parts, or damage that could affect the tester’s aesthetic appeal or functionality.
5. Ensuring Long-Term Stability in Performance
A reliable battery tester must not only perform well upon delivery but also maintain stable performance over time. To ensure long-term stability:
- Temperature and Humidity Control: Battery testers are designed to operate in a range of environmental conditions. However, extreme temperatures or humidity can affect performance. High-quality testers are designed with these environmental factors in mind and are subjected to rigorous testing for durability under various conditions.
- Robust Design: The internal components of the tester, including circuit boards and sensors, are built to withstand wear and tear. They are also shielded from interference and damage caused by external factors like dust, vibration, or accidental drops.
- Battery Management: For testers that rely on their own rechargeable batteries, longevity is essential. Manufacturers implement designs that optimize power consumption and prevent excessive wear on the internal battery.
6. Customer Feedback and Product Improvements
One of the most effective ways to ensure a product's quality and reliability is to incorporate customer feedback. Customers who use battery testers in real-world environments often encounter unique challenges or scenarios that the manufacturer might not have anticipated. By listening to user feedback, manufacturers can:
- Identify and Address Issues: If customers report issues with accuracy, ease of use, or durability, manufacturers can make improvements in future models or offer software updates to address these concerns.
- Enhance Features: Feedback on missing features or desired upgrades (e.g., new battery type compatibility or advanced testing modes) can inform the development of more versatile models.
- Provide Continuous Support: Customer feedback is also crucial for troubleshooting and support. Offering prompt customer service and troubleshooting guidance can extend the life of the product.
7. Regular Calibration and Maintenance for Reliable Use
To ensure continued reliability, regular calibration and maintenance are necessary. Over time, battery testers may experience small shifts in their measurements due to aging sensors or wear. Regular calibration ensures that the tester remains accurate throughout its lifespan.
- Calibration Frequency: The frequency of calibration depends on the model and its use. Some high-end testers may require recalibration annually, while others may maintain their accuracy for longer periods.
- Maintenance Services: For professional-grade testers, manufacturers may offer maintenance services to replace worn-out components or update software, ensuring that the tester continues to operate at peak performance.
8. Warranties and Customer Support for Quality Assurance
Most reputable manufacturers offer warranties to provide peace of mind to customers. These warranties typically cover defects in materials or workmanship, offering customers free repairs or replacements if the tester fails due to manufacturing issues. Additionally, robust customer support is essential for quality assurance:
- Product Support: Manufacturers often provide troubleshooting guides, FAQs, and instructional materials to help users get the most out of their battery testers.
- Repairs and Replacements: For testers that need repairs, quality manufacturers offer reliable repair services or replacement options, minimizing downtime for users.
9. Certifications and Independent Testing for Product Quality
Battery testers are often subjected to independent testing and certification to ensure they meet industry standards for quality and performance. These certifications can include:
- Safety Certifications: Compliance with international safety standards ensures that the tester is safe to use and will not pose any risks to the user or the batteries being tested.
- Environmental Certifications: Eco-friendly certifications demonstrate the manufacturer's commitment to sustainability, ensuring that the tester complies with environmental regulations and is made from recyclable materials.
- Performance Standards: Independent third-party tests may assess the accuracy and reliability of the tester in real-world conditions, providing confidence to users about the product's performance.
10. Continuous Innovation and Technology Upgrades
As battery technologies evolve, so too must the testers that monitor them. Continuous innovation in battery tester design is essential to stay ahead of advancements in battery technology. Manufacturers frequently upgrade their testers to support new battery chemistries, improve software functionality, and add features like wireless connectivity or cloud-based analysis.
By embracing cutting-edge technologies, battery tester manufacturers can enhance accuracy, user experience, and overall performance, ensuring their products remain relevant in a rapidly changing market.
11. Choosing a Reliable Battery Tester for Your Needs
When selecting a battery tester, it’s important to choose one that meets your specific needs. Consider the following:
- Battery Type Compatibility: Make sure the tester is compatible with the types of batteries you frequently test.
- Usage Environment: Choose a tester that is durable and easy to use in the environments where you plan to use it (e.g., automotive repair, industrial applications, home use).
- Features vs. Price: Determine what features are essential for your purposes, such as data logging or advanced testing modes, and find a tester that offers a balance of functionality and cost-effectiveness.
12. Conclusion: Ensuring Quality and Performance in Battery Testers
Ensuring the quality and performance of a battery tester requires a combination of rigorous manufacturing processes, quality control measures, customer feedback, and continuous innovation. By paying attention to key features like accuracy, durability, and compatibility, and by incorporating regular maintenance, calibration, and updates, manufacturers can create reliable battery testers that deliver consistent results.
Whether you are a professional in need of a high-precision tester or a consumer looking for an affordable solution, understanding these factors will help you make an informed decision and ensure the long-term stability and reliability of your battery tester.
Popular Battery Tester
Popular Battery Tester
Latest News
Latest News
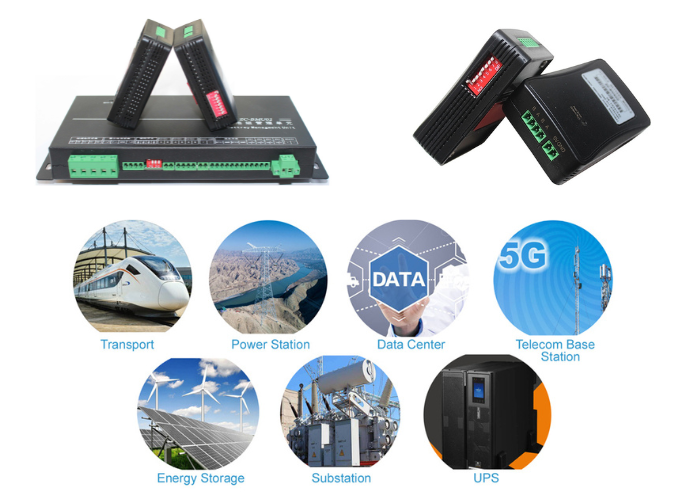
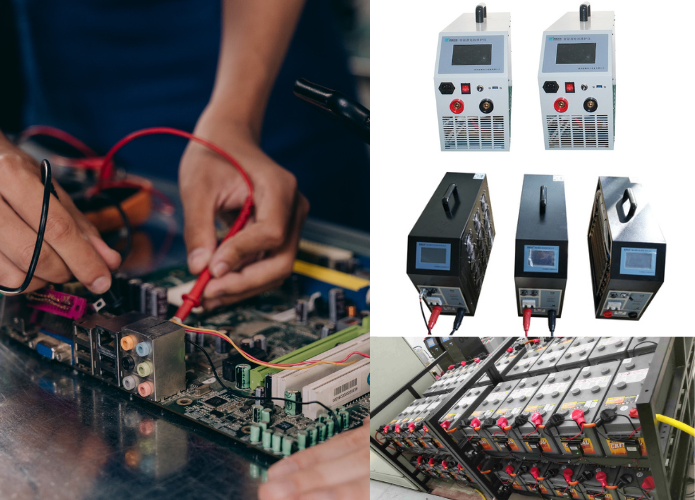
Get Price of Battery Tester
Get Price of Battery Tester
Address:
Floor 3, Building 1, No.1418-60, Moganshan road, Hangzhou city, Zhejiang Province, China.310015