Battery Management System: Everything You Need to Know
What is Battery Management System (BMS)?
A Battery Management System (BMS) is a critical technology designed to oversee and manage the operation of rechargeable battery packs. It encompasses a range of functions aimed at ensuring the safe, efficient, and reliable operation of batteries. Essentially, a BMS monitors the state of the battery, including parameters such as voltage, current, and temperature, and provides protection against conditions that could harm the battery or pose safety risks. This system plays a crucial role in optimizing the performance and lifespan of battery packs, which are integral to a wide array of applications from electric vehicles to renewable energy systems.
Importance of BMS in Modern Technology
In today’s technology-driven world, the importance of BMS cannot be overstated. As the demand for portable and sustainable energy solutions continues to rise, the reliance on rechargeable batteries has grown exponentially. Electric vehicles (EVs), for instance, are revolutionizing the transportation industry by providing an eco-friendly alternative to fossil fuel-powered cars. The success and adoption of EVs hinge significantly on the efficiency and safety provided by advanced BMS technologies. Similarly, in renewable energy systems, BMS ensures the optimal storage and utilization of energy generated from intermittent sources like solar and wind, thereby enhancing energy reliability and sustainability.
Moreover, consumer electronics such as smartphones, laptops, and wearable devices rely on battery packs for power. A robust BMS ensures these devices operate safely and effectively, preventing potential hazards like overheating and battery fires. Industrial applications, aerospace, and defense sectors also benefit from the reliability and precision of advanced BMS, which support critical operations and enhance overall system performance. Thus, BMS technology is pivotal in driving innovation and sustainability across various sectors.
Overview of BMS Functions
The functions of a BMS are multifaceted and encompass several key areas, including monitoring, protection, balancing, state estimation, and communication. Monitoring involves continuously measuring key parameters such as voltage, current, and temperature of individual cells within the battery pack. This real-time data collection is crucial for assessing the battery’s condition and performance. Protection mechanisms are integral to a BMS, safeguarding the battery from conditions like over-voltage, under-voltage, over-temperature, and over-current, which could potentially damage the battery or pose safety risks.
Balancing is another critical function, ensuring that all cells within the battery pack are charged uniformly, thereby preventing imbalance-related issues and enhancing the overall efficiency and lifespan of the battery. State estimation involves calculating important metrics such as State of Charge (SOC), State of Health (SOH), and State of Power (SOP). These metrics provide valuable insights into the battery’s current status and its remaining useful life. Lastly, communication functions allow the BMS to interface with other system components, both within the battery pack and with external devices, facilitating coordinated operation and data exchange.
Components of a Battery Management System
1. Battery Cells and Modules
At the core of any Battery Management System (BMS) are the battery cells and modules. A battery pack is composed of multiple individual cells, which are grouped into modules. Each cell is a fundamental unit that stores and releases electrical energy through electrochemical reactions. These cells can vary in chemistry, form factor, and capacity, and they are connected in series and parallel configurations to achieve the desired voltage and capacity for the application. The arrangement of cells into modules facilitates efficient management, monitoring, and replacement if necessary. Ensuring the cells are properly balanced and monitored is crucial for maintaining the overall health and efficiency of the battery pack.
2. BMS Hardware Components
* Microcontroller/Processor
The microcontroller or processor is the brain of the BMS. It is responsible for executing the software algorithms that monitor, control, and manage the battery pack. The microcontroller processes data from various sensors and makes real-time decisions to ensure the safe and optimal operation of the battery. This includes calculating key metrics such as State of Charge (SOC) and State of Health (SOH), as well as implementing protection strategies to prevent harmful conditions.
* Sensors (Voltage, Temperature, Current)
Sensors are critical components of a BMS, providing the necessary data to monitor the battery pack’s status. Voltage sensors measure the voltage of individual cells and the overall pack, ensuring they remain within safe operating limits. Temperature sensors monitor the temperature of cells and modules, as extreme temperatures can affect battery performance and safety. Current sensors measure the current flowing in and out of the battery pack, providing data for energy flow management and state estimation algorithms. Accurate sensing is essential for effective monitoring and control of the battery pack.
* Communication Interfaces
Communication interfaces enable the BMS to exchange data with other system components and external devices. These interfaces can include wired connections, such as CAN bus, I2C, SPI, and UART, as well as wireless communication technologies. Effective communication allows the BMS to share information about the battery’s status, receive commands, and integrate with higher-level control systems, such as those in electric vehicles or renewable energy storage systems. Reliable and fast communication is vital for coordinated operation and ensuring the safety and performance of the battery pack.
* Balancing Circuits
Balancing circuits are used to equalize the charge across all cells in the battery pack. Over time, cells can become imbalanced, meaning some cells may have higher or lower charge levels compared to others. This imbalance can lead to reduced overall performance and capacity, as well as potential safety risks. There are two primary types of balancing: passive and active. Passive balancing dissipates excess energy from higher-charged cells as heat, while active balancing redistributes energy from higher-charged cells to lower-charged ones. Effective balancing extends the life and efficiency of the battery pack.
3. BMS Software Components
* Firmware
Firmware is the software embedded in the BMS hardware that controls its operations. It includes the basic instructions and algorithms necessary for the BMS to function correctly. Firmware handles tasks such as data acquisition from sensors, execution of control algorithms, and communication with other devices. It is designed to operate in real-time, ensuring that the BMS can respond quickly to changes in the battery’s state and environment. Firmware updates can improve BMS performance and add new features, making it a critical component of the system.
* Algorithms (State of Charge, State of Health)
Advanced algorithms are essential for accurately estimating the battery’s State of Charge (SOC) and State of Health (SOH). SOC algorithms determine the remaining charge in the battery, which is crucial for energy management and predicting the range in electric vehicles. SOH algorithms assess the battery’s overall condition and remaining useful life, providing insights into its performance and longevity. These algorithms use data from sensors and historical usage patterns to make precise calculations. Accurate state estimation ensures that the battery operates within safe limits and performs optimally throughout its lifespan.
The components of a Battery Management System, encompassing both hardware and software elements, work together to ensure the safe, efficient, and reliable operation of battery packs. These components are integral to managing the complexities of modern battery technology and are critical in applications ranging from electric vehicles to renewable energy systems.
Functions of a Battery Management System
1. Monitoring
* Voltage Monitoring
Voltage monitoring is a critical function of a Battery Management System (BMS). The BMS continuously measures the voltage of individual cells and the overall battery pack. This data is essential for determining the state of charge, detecting imbalances among cells, and identifying potential issues such as over-voltage or under-voltage conditions. Accurate voltage monitoring helps ensure the battery operates within safe limits and maintains optimal performance.
* Temperature Monitoring
Temperature monitoring is vital for the safety and efficiency of the battery pack. The BMS uses temperature sensors to track the temperature of individual cells and modules. Extreme temperatures, whether too high or too low, can negatively impact battery performance and longevity. By monitoring temperature, the BMS can implement cooling or heating strategies to keep the battery within its optimal operating range, thus preventing thermal runaway and extending the battery’s lifespan.
* Current Monitoring
Current monitoring involves measuring the flow of electric current into and out of the battery pack. This information is crucial for managing energy flow, estimating the state of charge, and ensuring the battery is not subjected to damaging current levels. The BMS uses current data to protect the battery from over-current conditions, which can lead to overheating and potential damage. Additionally, current monitoring supports accurate energy accounting and helps in diagnosing potential issues.
2. Protection
* Over-Voltage Protection
Over-voltage protection safeguards the battery from excessive voltage levels that can cause damage to the cells. The BMS monitors the voltage of each cell and the overall pack and takes action if the voltage exceeds safe thresholds. This may involve disconnecting the battery from the charging source or triggering an alarm to alert users. Over-voltage protection is crucial for preventing cell degradation and ensuring the battery’s safety and longevity.
* Under-Voltage Protection
Under-voltage protection prevents the battery from being discharged below a safe voltage level. Excessive discharge can lead to cell damage, reduced capacity, and decreased overall performance. The BMS monitors cell voltages and disconnects the load or triggers an alert if the voltage drops below a predetermined threshold. This function helps preserve the health and lifespan of the battery by avoiding deep discharge conditions.
* Over-Temperature Protection
Over-temperature protection ensures the battery does not exceed safe operating temperatures. High temperatures can lead to thermal runaway, where the battery rapidly heats up, potentially causing fires or explosions. The BMS monitors cell temperatures and activates cooling systems, reduces current flow, or shuts down the battery pack if temperatures rise above safe limits. This protection mechanism is essential for maintaining battery safety and performance.
* Over-Current Protection
Over-current protection guards against excessive current flow that can damage the battery cells and circuitry. The BMS monitors the current and takes action, such as reducing the load or disconnecting the battery, if the current exceeds safe levels. Over-current protection helps prevent overheating, cell damage, and potential safety hazards, ensuring the battery operates within its designed current limits.
3. Balancing
* Passive Balancing
Passive balancing involves dissipating excess energy from higher-charged cells as heat to equalize the charge across all cells in the battery pack. This method uses resistors to discharge the higher-charged cells, bringing them into balance with lower-charged cells. While passive balancing is relatively simple and cost-effective, it is less efficient than active balancing as it wastes energy as heat.
* Active Balancing
Active balancing redistributes energy from higher-charged cells to lower-charged ones, achieving charge equalization without significant energy loss. This method uses inductors, capacitors, or transformers to transfer energy between cells. Active balancing is more efficient than passive balancing and helps extend the battery pack’s overall efficiency and lifespan by ensuring all cells are equally charged.
4. State Estimation
* State of Charge (SOC)
State of Charge (SOC) estimation determines the remaining charge in the battery, expressed as a percentage of its total capacity. Accurate SOC estimation is crucial for managing energy usage, predicting the range of electric vehicles, and optimizing charging cycles. The BMS uses data from voltage, current, and temperature sensors, along with complex algorithms, to calculate the SOC in real-time.
* State of Health (SOH)
State of Health (SOH) estimation assesses the overall condition and remaining useful life of the battery. SOH provides insights into the battery’s capacity, efficiency, and performance degradation over time. The BMS uses historical data, usage patterns, and sensor measurements to estimate the SOH, helping to predict maintenance needs and replacement timing, and ensuring reliable battery operation.
* State of Power (SOP)
State of Power (SOP) estimation determines the battery’s ability to deliver power under specific conditions. It takes into account factors such as SOC, temperature, and internal resistance to predict the maximum power output and input the battery can handle. SOP estimation is crucial for applications requiring high power delivery, such as electric vehicles, ensuring the battery can meet performance demands without compromising safety or longevity.
5. Communication
* Internal Communication (Within the Battery Pack)
Internal communication refers to the data exchange between the BMS and individual cells or modules within the battery pack. This communication ensures the BMS can monitor and manage each cell’s status, perform balancing, and implement protection strategies. Internal communication typically uses wired protocols such as CAN bus, I2C, or SPI, providing reliable and fast data transfer for real-time monitoring and control.
* External Communication (With External Devices)
External communication involves the BMS interfacing with external devices, such as vehicle control systems, charging stations, or energy management systems. This communication allows the BMS to share information about the battery’s status, receive control commands, and integrate with other system components. External communication can use wired connections, such as CAN bus or Ethernet, as well as wireless technologies. Effective external communication ensures coordinated operation, enhances system efficiency, and supports remote monitoring and diagnostics.
Types of Battery Management Systems
1. Centralized BMS
A centralized Battery Management System (BMS) is characterized by a single controller that manages and monitors all the battery cells in a pack. In this system, all the sensors and monitoring circuits are directly connected to the central controller. This configuration simplifies the design and reduces the complexity of communication, as all data is processed in one location. However, centralized BMS can be less scalable and may present challenges in terms of wiring complexity, especially for large battery packs. Additionally, the central controller becomes a single point of failure, which can affect the reliability of the system.
2. Distributed BMS
A distributed BMS employs multiple controllers, each responsible for a subset of the battery cells. Each controller manages a small group of cells and communicates with a master controller that coordinates the entire system. This approach reduces the complexity of wiring and allows for better scalability, making it suitable for large battery packs. Distributed BMS can improve reliability, as the failure of a single controller affects only a small part of the system rather than the entire battery pack. This type of system is particularly advantageous for applications with large and complex battery configurations, such as electric vehicles and grid storage systems.
3. Modular BMS
A modular BMS combines elements of both centralized and distributed systems, offering a flexible and scalable solution. In this system, the battery pack is divided into modules, each with its own BMS unit that monitors and manages the cells within that module. These modular BMS units communicate with a central controller or among themselves, forming a cohesive system. This modular approach allows for easier maintenance and replacement of individual modules, enhancing the overall reliability and serviceability of the battery pack. Modular BMS is ideal for applications where flexibility and scalability are important, such as in electric vehicles and renewable energy storage systems, where battery packs may need to be customized or expanded over time.
The type of Battery Management System used can significantly impact the efficiency, scalability, and reliability of a battery pack. Centralized BMS offers simplicity but may struggle with large packs, distributed BMS improves scalability and reliability for complex systems, and modular BMS provides a flexible and maintainable solution suitable for a wide range of applications.
Applications of Battery Management Systems
1. Electric Vehicles (EVs)
Battery Management Systems (BMS) are crucial for the operation of electric vehicles (EVs). In EVs, the BMS ensures the optimal performance, safety, and longevity of the battery pack, which is the most expensive and critical component of the vehicle. The BMS monitors the state of charge (SOC), state of health (SOH), and temperature of the battery cells, ensuring they operate within safe limits. It also performs cell balancing to maintain uniform charge levels across all cells, preventing premature degradation and extending the overall lifespan of the battery. Additionally, the BMS protects against conditions like over-voltage, under-voltage, over-current, and overheating, which can cause damage or safety hazards. By managing these factors, the BMS plays a pivotal role in enhancing the range, efficiency, and reliability of EVs.
2. Renewable Energy Storage Systems
In renewable energy storage systems, such as those used for solar and wind power, a BMS is essential for managing large battery banks that store and distribute energy. The BMS ensures that the energy storage system operates efficiently and safely, providing reliable power even when renewable sources are intermittent. It monitors the charge and discharge cycles, balances the cells, and protects against extreme conditions that could damage the battery pack. By doing so, the BMS helps maximize the lifespan and performance of the energy storage system, making renewable energy solutions more viable and sustainable. Effective BMS integration allows for better energy management, load balancing, and grid stabilization, supporting the broader adoption of renewable energy technologies.
3. Consumer Electronics
In consumer electronics, such as smartphones, laptops, and wearable devices, the BMS is responsible for ensuring safe and efficient battery operation. The BMS monitors the battery's voltage, temperature, and charge status, providing accurate SOC and SOH estimates to users. It also implements protection mechanisms to prevent overcharging, deep discharging, and overheating, which can reduce battery life and pose safety risks. By managing these aspects, the BMS helps enhance the performance, reliability, and user experience of consumer electronics. Moreover, advances in BMS technology contribute to longer battery life, faster charging, and better energy efficiency in these devices.
4. Industrial Applications
Industrial applications, such as uninterruptible power supplies (UPS), forklifts, and automated guided vehicles (AGVs), rely heavily on robust and reliable battery systems. A BMS in these applications ensures that the battery packs operate safely and efficiently under demanding conditions. It monitors the battery's health and performance, balances the cells, and protects against potential issues like overloading and overheating. In critical applications like UPS, the BMS guarantees continuous power supply during outages, while in AGVs and forklifts, it ensures reliable operation and minimizes downtime. By providing accurate data and diagnostics, the BMS helps maintain optimal battery performance and extend operational lifespan, which is crucial for industrial efficiency and productivity.
5. Aerospace and Defense
In aerospace and defense applications, battery reliability and safety are of utmost importance. A BMS in these fields manages complex battery systems used in applications such as satellites, drones, military vehicles, and portable power supplies. It ensures that the batteries operate within safe parameters, providing critical monitoring and protection against failure modes that could jeopardize missions or safety. The BMS also offers precise state estimation and diagnostics, which are essential for mission planning and operational readiness. Advanced BMS technologies support the high energy density and reliability required in aerospace and defense applications, ensuring that battery systems meet stringent performance and safety standards.
Battery Management Systems are integral to a wide range of applications, from electric vehicles and renewable energy storage to consumer electronics, industrial equipment, and aerospace and defense. They ensure the safe, efficient, and reliable operation of battery packs, supporting the advancement and adoption of battery-powered technologies across various sectors.
Challenges and Solutions in BMS Design
1. Thermal Management
Challenge:
Thermal management is a significant challenge in BMS design due to the heat generated during battery charging and discharging cycles. Excessive heat can lead to thermal runaway, where temperatures rise uncontrollably, potentially causing fires or explosions. Maintaining optimal temperature ranges is crucial for battery performance, safety, and longevity.
Solution:
Effective thermal management strategies include the use of advanced cooling systems, such as liquid cooling, air cooling, or phase-change materials, to dissipate heat efficiently. The BMS can incorporate thermal sensors to monitor the temperature of individual cells and the entire pack in real-time. Additionally, thermal management algorithms can predict and manage thermal loads by adjusting charge/discharge rates or activating cooling mechanisms when necessary. Integrating thermal management into the BMS ensures that temperatures remain within safe limits, enhancing the overall safety and efficiency of the battery system.
2. Accuracy in State Estimation
Challenge:
Accurately estimating the state of charge (SOC), state of health (SOH), and state of power (SOP) is challenging due to the complex and nonlinear behavior of batteries. Inaccurate estimations can lead to improper battery management, reducing performance and lifespan.
Solution:
Improving state estimation accuracy involves using advanced algorithms and models that consider various factors such as voltage, current, temperature, and historical usage data. Techniques like Kalman filtering, machine learning, and neural networks can enhance the precision of SOC, SOH, and SOP estimations. Regular calibration and validation of these algorithms with real-world data also help maintain accuracy. High-quality sensors and data acquisition systems are essential for providing reliable inputs to these estimation algorithms, ensuring that the BMS can make precise and informed decisions.
3. Scalability
Challenge:
Designing a BMS that can scale effectively with varying sizes of battery packs, from small consumer electronics to large industrial systems, poses a significant challenge. Scalability affects the complexity of wiring, communication, and overall system architecture.
Solution:
Adopting a modular BMS design can address scalability issues. In a modular approach, the battery pack is divided into smaller, manageable units, each with its own BMS unit that can operate independently or in coordination with others. This design simplifies wiring and enhances flexibility, allowing for easy expansion or reconfiguration of the battery pack. Implementing standardized communication protocols and interfaces ensures seamless integration between modules and the central controller. Scalability is further supported by using distributed BMS architectures, where multiple controllers manage different sections of the battery pack, enabling efficient handling of large-scale systems.
4. Reliability and Safety
Challenge:
Ensuring the reliability and safety of the BMS is critical, especially in applications where failure can have severe consequences, such as in electric vehicles or aerospace. The BMS must protect against various failure modes and operate reliably under diverse conditions.
Solution:
To enhance reliability and safety, the BMS should incorporate robust fault detection and mitigation mechanisms. Redundant systems and fail-safe designs can help maintain functionality even if part of the system fails. Regular diagnostics and self-check routines ensure the BMS can identify and address issues promptly. The use of high-quality, durable components and rigorous testing under different environmental conditions also contribute to system reliability. Safety can be further ensured by adhering to industry standards and regulations, such as ISO 26262 for automotive systems, which provide guidelines for functional safety in BMS design.
5. Cost Considerations
Challenge:
Cost is a critical factor in BMS design, as it directly impacts the affordability and market competitiveness of battery-powered products. Balancing the need for advanced features and high performance with cost-effectiveness can be challenging.
Solution:
Cost-effective BMS design involves optimizing the selection and use of components, focusing on high-impact areas such as sensors, processors, and communication interfaces. Leveraging economies of scale in manufacturing and using modular designs can reduce production costs. Simplifying the BMS architecture without compromising essential functionalities can also help lower costs. Additionally, implementing software solutions and algorithms that maximize the efficiency and lifespan of the battery can provide long-term cost benefits by reducing the need for frequent replacements and maintenance. Strategic partnerships and investments in research and development can drive innovation while keeping costs manageable.
Addressing the challenges in BMS design requires a comprehensive approach that includes advanced technologies, robust engineering practices, and cost-effective solutions. By tackling issues such as thermal management, state estimation accuracy, scalability, reliability, and cost, BMS designers can create systems that enhance the safety, performance, and affordability of battery-powered applications across various industries.
Future Trends in Battery Management Systems
1. Advances in Battery Technology
As battery technology continues to evolve, future Battery Management Systems (BMS) will need to adapt to new types of batteries with improved performance characteristics. Advances in solid-state batteries, lithium-sulfur, and lithium-air technologies promise higher energy densities, longer lifespans, and safer operation compared to traditional lithium-ion batteries. BMS will play a crucial role in maximizing the potential of these advanced batteries by providing precise monitoring, control, and optimization tailored to the unique properties of each new battery chemistry. Enhanced algorithms and sensor technologies will be necessary to manage these next-generation batteries effectively, ensuring they deliver their full potential in various applications.
2. Integration with Internet of Things (IoT)
The integration of BMS with the Internet of Things (IoT) represents a significant trend that will transform how batteries are managed and utilized. IoT-enabled BMS can connect to cloud platforms and other devices, facilitating remote monitoring, diagnostics, and control. This connectivity allows for real-time data collection and analysis, providing insights into battery performance and health across multiple systems and locations. IoT integration enables predictive maintenance, where potential issues can be identified and addressed before they lead to failures, thus enhancing reliability and reducing downtime. Moreover, it supports energy management systems by allowing seamless coordination between various energy sources and storage solutions, optimizing energy usage and improving overall efficiency.
3. Artificial Intelligence (AI) in BMS
Artificial Intelligence (AI) is poised to revolutionize BMS by providing advanced analytics and decision-making capabilities. AI algorithms can process vast amounts of data from battery operations to identify patterns, predict behavior, and optimize performance. Machine learning techniques can enhance state estimation accuracy, improve fault detection, and enable adaptive control strategies that respond dynamically to changing conditions. AI can also optimize charging and discharging cycles, extending battery life and improving efficiency. The integration of AI into BMS will lead to smarter, more autonomous systems capable of managing complex battery packs with minimal human intervention, thus advancing the capabilities of electric vehicles, renewable energy systems, and other battery-dependent technologies.
4. Wireless BMS
Wireless BMS represents a significant advancement in simplifying battery pack design and enhancing scalability. Traditional BMS requires extensive wiring to connect sensors and control units, which can be complex and prone to issues in large battery packs. Wireless BMS eliminates the need for physical connections by using wireless communication protocols to transmit data between cells and the central controller. This innovation reduces wiring complexity, weight, and installation time while improving flexibility and scalability. Wireless BMS can also enhance safety by isolating cells more effectively and allowing for easier maintenance and reconfiguration of battery packs. As wireless communication technologies continue to improve, wireless BMS will become increasingly viable and prevalent in various applications.
5. Enhanced Safety Features
Future BMS will incorporate enhanced safety features to address the increasing demand for reliable and secure battery systems. These features will include more sophisticated fault detection and mitigation strategies, such as real-time monitoring of internal cell conditions and advanced thermal management techniques. Safety algorithms will be improved to detect and respond to a broader range of potential issues, including internal shorts and external impacts. Enhanced safety features will also involve better integration with external safety systems, such as vehicle crash detection in electric vehicles, to ensure comprehensive protection. As battery technology advances and applications become more demanding, the emphasis on safety will continue to grow, driving innovations in BMS design and functionality.
The future of Battery Management Systems will be shaped by significant technological advancements and integrations. Progress in battery technology, IoT connectivity, AI, wireless systems, and safety features will drive the evolution of BMS, making them more intelligent, efficient, and reliable. These trends will enable BMS to better support the growing and diverse applications of batteries, from electric vehicles to renewable energy storage and beyond.
Conclusion
Battery Management Systems (BMS) are indispensable in modern technology, providing the necessary oversight and control to ensure the safe, efficient, and reliable operation of battery packs across a wide range of applications. From electric vehicles and renewable energy storage systems to consumer electronics, industrial applications, and aerospace and defense, BMS play a crucial role in optimizing battery performance and longevity.
The key functions of BMS, including monitoring, protection, balancing, state estimation, and communication, are critical for maintaining the health and efficiency of batteries. Challenges such as thermal management, accurate state estimation, scalability, reliability, and cost considerations require innovative solutions to ensure BMS can meet the demands of increasingly sophisticated battery technologies.
Looking forward, the future of BMS will be shaped by several exciting trends. Advances in battery technology will necessitate more advanced BMS capabilities. Integration with the Internet of Things (IoT) will enable real-time data analysis and predictive maintenance. Artificial Intelligence (AI) will bring smarter, more autonomous BMS operations. Wireless BMS will simplify design and improve scalability, and enhanced safety features will provide comprehensive protection for ever-more-demanding applications.
In conclusion, the ongoing evolution of BMS technology will continue to enhance the safety, efficiency, and reliability of battery-powered systems, driving progress in numerous fields and supporting the broader adoption of sustainable energy solutions. The development of advanced BMS is essential to unlocking the full potential of emerging battery technologies and meeting the growing energy demands of the future.
Popular Battery Tester
Popular Battery Tester
Latest News
Latest News
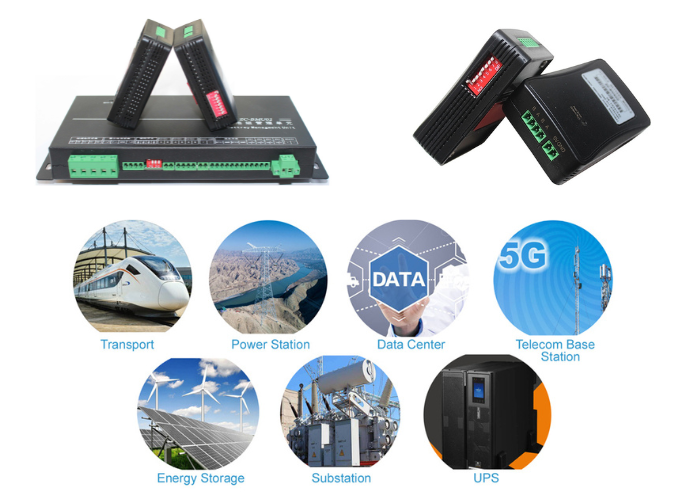
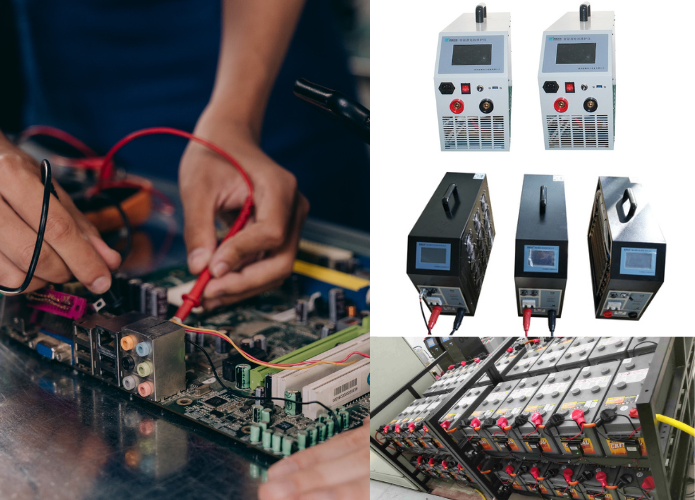
Get Price of Battery Tester
Get Price of Battery Tester
Address:
Floor 3, Building 1, No.1418-60, Moganshan road, Hangzhou city, Zhejiang Province, China.310015